Fracture, Damage, and Impact Mechanics
Computational Materials Modeling, Virginia Tech
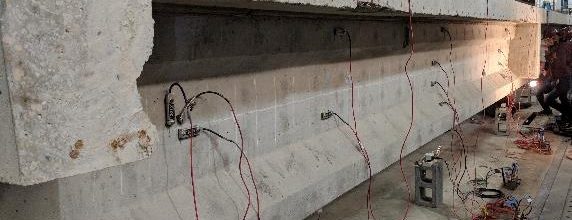
The science- and physics-based computational models of failure criteria, crack initiation, propagation, and fatigue damage under different static or dynamic loads to revolutionize component designs.
Faculty
David Dillard, Computational Materials Modeling, Virginia Tech
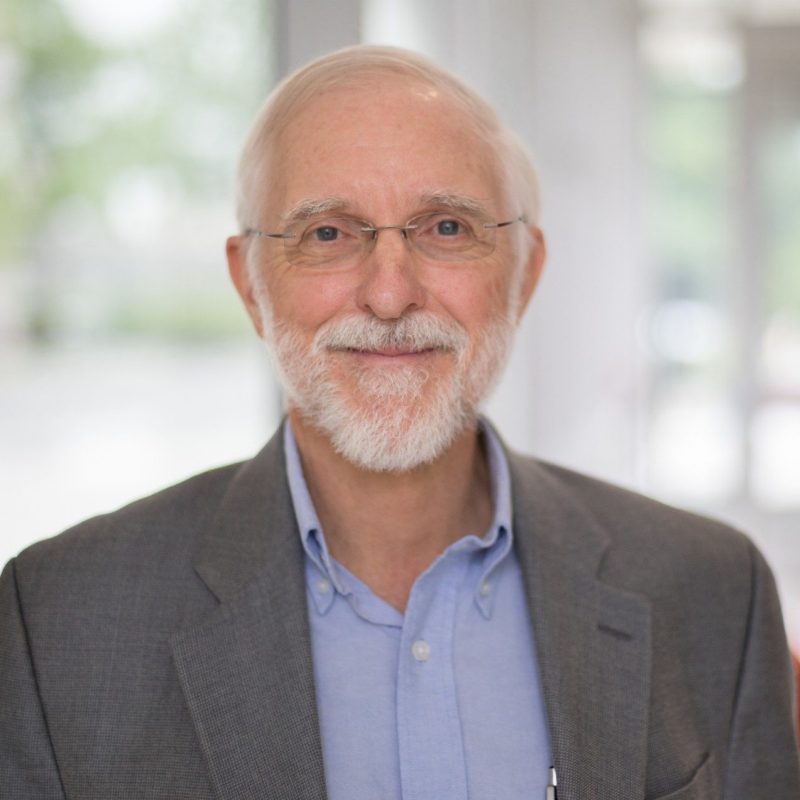
David Dillard
David Dillard has worked extensively in the field of adhesive bonding, having experience in structural, microelectronic, and construction applications of adhesives, coatings, sealants, and membranes. With over 190 refereed publications, his computational solutions are often paired with experimental results for a wide range of adhesion and adhesive bond challenges.
Gary Seidel, Computational Materials Modeling, Virginia Tech
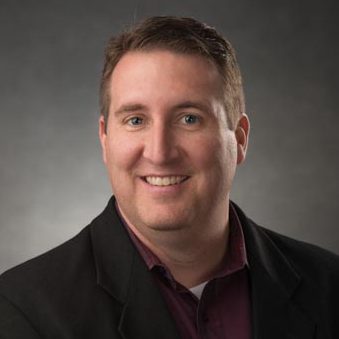
Gary Seidel
Focus on multiscale modeling of damage initiation and progression in multifunctional composites from atomistic length and time scales (interface strength), through micro- and mesoscales in composites (microdamage), to applications/structures at the macroscale (fracture). Emphasis on sensing strain and damage evolution in nanocomposite-enriched structures and materials under dynamic loads via piezoresistivity.
Ioannis Koutromanos, Computational Materials Modeling, Virginia Tech
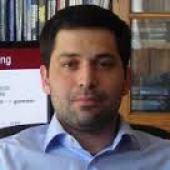
Ioannis Koutromanos
My research is focused on computational simulation of material and structural failure under extreme loading events through constitutive modeling of engineering materials, finite element analysis and reduced-order models. Additionally, I am investigating the impact of structural aging on civil infrastructure through coupled, multi-physics simulations.
Kevin Wang, Computational Materials Modeling, Virginia Tech
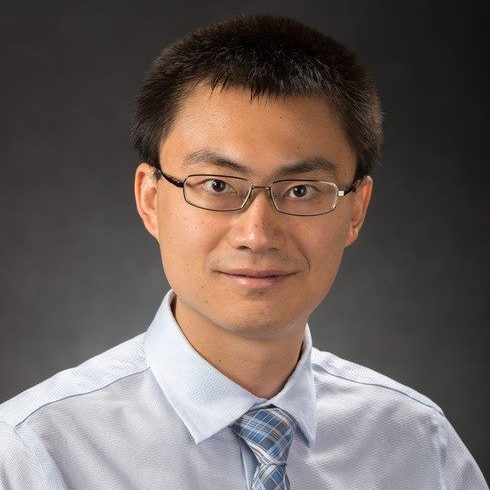
Kevin Wang
The Multiphysics Modeling and Computation (M2C) Lab focuses on the development of new models, algorithms, and computer programs for simulating engineering and health-related problems involving multiple physical domains, multiple physical fields, and/or different length and time scales. Our areas of expertise include fluid-solid interaction, shock waves, and multiscale material modeling.
Ling Li, Computational Materials Modeling, Virginia Tech
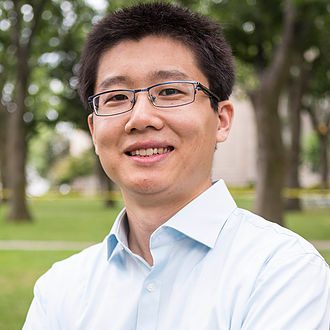
Ling Li
Area 1:
Organisms are constructed with many remarkable structural materials. We aim to uncover the fundamental material design rules of biological structural and multifunctional materials (such as 3D fiber composites, foams, armor materials, etc.) through multiscale 3D structural and mechanical quantification and modeling, and design and fabricate bio-inspired analogs for engineering applications.
Area 2:
Biomineralized materials (shells, teeth, sponges, etc.) often exhibit hierarchical 3D structural designs, contributing to their unique mechanical and other properties. We aim to understand the underlying formation mechanisms of selected biomineralized structures (e.g., the biomineralized photonic structure in blue-rayed limpets) through in-vitro and in-vivo quantitative 3D structural analysis and modeling.
Maryam Shakiba, Computational Materials Modeling, Virginia Tech
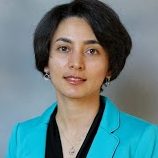
Maryam Shakiba
We focus on multi-physics and multi-scale simulation of heterogeneous materials to unravel the link between the composition and performance of composites with soft and dissipative properties. We integrate damage mechanics, thermodynamic laws, sensitivity analyses, and computational methods to study materials behavior under coupled moisture, chemical, temperature, and mechanical conditions.
Raffaella De Vita, Computational Materials Modeling, Virginia Tech
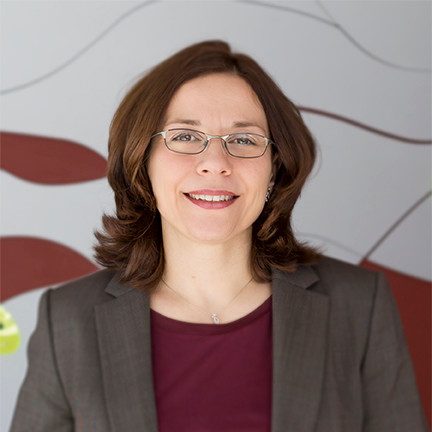
Raffaella De Vita
Mechanical properties characterization of biological systems ranging from cellular components to tissues, with special emphasis on the development of new mathematical models and experimental methods.
Rakesh Kapania, Computational Materials Modeling, Virginia Tech
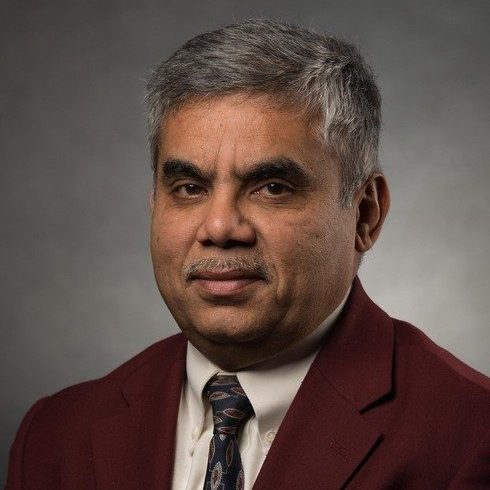
Rakesh K. Kapania
Dr. Kapania's research involves local/global analysis and optimization to design thin-walled structural, stiffened components using curvilinearly stiffened elements that can ow be fabricated using additive manufacturing and composite panels with curvilinear stiffeners. He has more than 35 years of experience in the area of computational structural mechanics with emphasis on laminated and metallic plates and shells, aeroelastic tailoring and inverse problems.
Reza Mirzaeifar, Computational Materials Modeling, Virginia Tech
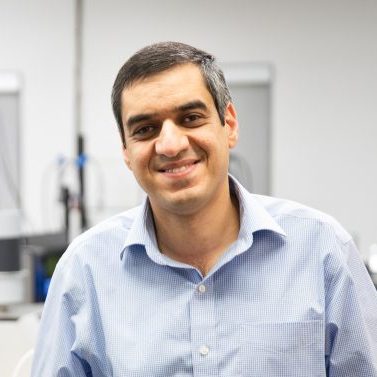
Reza Mirzaeifar
In MultiScale Mechanics of Advanced Materials Laboratory (MultiSMArt) we use a wide range of theoretical, computational and experimental methods at different length scales to study the mechanics of various advanced materials including shape memory alloys, carbon-based materials, biological and bio-inspired materials, composites and soft materials.
Scott Case, Computational Materials Modeling, Virginia Tech
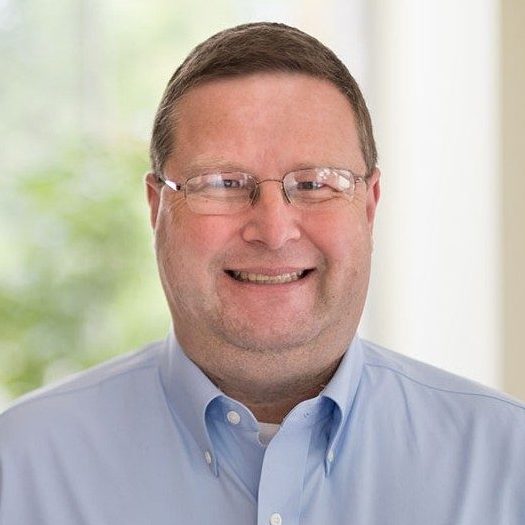
Scott Case
Professor Case's work combines experiments, analysis, and simulations to examine the performance and durability of materials and structures. Example applications include optimizing the designs of energy absorbing structures and predicting strength of advanced composites using Monte Carlo simulations. In the multiphysics area, Professor Case has been examining the response of lightweight structures to combined fire and mechanical loading.